Doing things better sometimes means starting at the very beginning. Developers, Colgan Industries in partnership with award winning architect Philip McAllister, have done just that with Square One apartments in Perth. From the outset, their goal has been to create a village style development that promotes a more sustainable future; this has been achieved by the adoption of the following practices or technologies.
Energy Efficiencies >
 |
Communal PV System - 10kW communal photo-voltaic solar arrays to feed the communal power needs of the complex, this includes – lighting, lifts, mechanical services in the basement, rainwater harvesting pumps and hot water circulating pumps. |
 |
Individual PV Systems – every apartment has the infrastructure (rails to roof and conduit from roof to the location of the inverter, and cabling back to the apartment sub-board) included that allows for the installation of a 1.08kW photo-voltaic solar array. All apartments have bi-directional meters installed. Currently 26 of the 35 apartments have installed a system. If the office and café were also to install their respective 5kW systems on top of the 10kW communal system there would be a total capacity of 55kW being generated by the complex.
|
 |
Solar Gas Boosted Hot Water System – rather than traditional electric storage units all apartments including the commercial tenancies are fed from a centrally located solar gas boosted hot water system. The system uses evacuated glass tubes, storage tanks and Bosch instantaneous boosters.
8 manifolds of 30 tube Apricus glass evacuated tubes
8 x 315 litre stainless steel tanks to hold pre-heated water
2 x Bosch 32 Commercial instantaneous gas boosters
attached to 315 litre storage tanks.
|
 |
North facing living areas –
29 of the 35 apartments (82%) have northerly aspects to
their living and kitchen areas and
32 of the 35 apartments (91%) have northerly aspects if
their enclosed indoor / outdoor living areas are included.
|
 |
Lighting – All external façade lighting LED lights – 6 watts - 2 x 3W up down lights with 7 year warranty
All bulkhead kitchen lights and main entry lights are from Brightgreen, an Australian firm. The D900 LED (16W) downlight is an equivalent in terms of light quality, strength and beam width to a 50W halogen. Expect 70,000 lamp hours or 24 years with 8 hours operation per day. Payback period of approximately 3 years based on 8 hours of use per day and current electricity tariffs.
Extensive use of compact fluorescents and T5 fluorescents both in the apartments and common areas. |
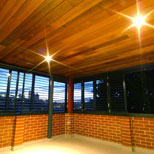 |
Louvres – extensive use of use of louvers to all elevations of the building for both control of solar gain and to meet privacy requirements.
Cross ventilation – 32 of 35 apartments have cross ventilation with the remaining 3 having large sets of glass sliding doors.
Electrically operated high level south glazing for heat dumping to loft / mezzanine apartments along the southern and northern sides of the project.
Insulation – Use of R3.0 batts and 50mm anti-con to all roof areas |
Water Efficiencies >
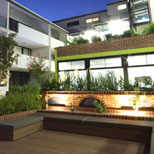 |
Rain Water Harvesting - saves approximately 530,000 litres of water per annum from mains sources. Located under the central courtyard garden is a 110,000 litre rainwater tank that collects from the complex’s roof which is then used in the toilets and washing machines of all apartments and the communal gardens. |
 |
Separate Remote Metering - of hot, cold and rain water harvesting to all apartments with daily consumption figures automatically sent, by email, to the strata manager. Billing is automatically generated for the strata manager by Billing Maid – www.billingmaid.com making this incredibly simple for the strata or building manager.
|
 |
Water Wise and Edible Garden – The garden has been designed by Josh Byrne from Josh Byrne and Associates to be both water wise and for the most part edible. A Netafim sub-soil drip irrigation system is utilized and ‘zoned’ for the different areas. Approximately 70% of the plants are edible being either fruit, vegetables or herbs and are free to be used by all residents.
|
 |
Fixtures –
Toilets dual flush – 4.5 / 3.0 Litre flushes
Basin mixers - 5.5 l/pm
Kitchen and laundry mixers – 7.5 l/pm
Shower heads – 9 l/pm.
|
Indoor Air Quality >
 |
Use of 100% Australian natural wool carpets mechanically fixed
Choice of natural granite tops and Caesar Stone
Kitchen and bathroom cabinetry – Local E1 particle board
Cross ventilation - 32 of 35 apartments have cross ventilation with the remaining 3 having large sets of glass sliding doors.
|
Resource Recovery >
 |
Peat - all peat excavated from the site was either transported and used by,
Turf farms and market gardens,
or
stockpiled to later be re-used and blended with soil for the project’s central courtyard and roof top gymnasium garden.. |
 |
The vast majority of the existing heritage masonry elements of the building were restored (facades) and / or converted in to living space. Those elements that were demolished, the bricks were salvaged and re-used along the Little Parry Street façade, the balance have been stored and will be used in future restoration projects.
The eastern boundary wall in the central courtyard and the southern boundary wall near the entry are retained original walls.
The first floor suspended slabs in the original 1928 portion of the building were retained and re-used.
|
 |
The original timber trusses were either re-used in the refurbishment of a secondary warehouse to the east of the site or used as vertical feature elements in the central courtyard.
All Sheoak stair treads and handrails were salvaged and machined from the clearing for the extensions to the South West Highway.
All suitable steel from the demolition was taken to the recyclers.
|
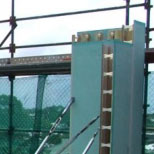 |
Approximately 90% of new walls are constructed from the Ritek XL wall system. This system is manufactured to order in a factory from shop drawings and shipped to site for erection. It is a form of permanent formwork that requires minimal finishing.
It –
Reduces waste to landfill as it is made to order.
Reduces water usage as no water is used in the manufacturing process and no water is required in the erection process. |
|
|
 |